Advanced Study and Technological Optimization of High-Frequency Vibration Tables in Product Reliability Testing
Abstract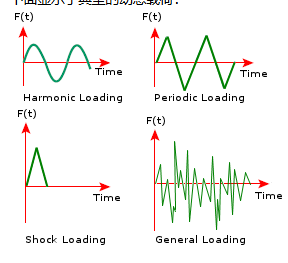
This study presents an in-depth analysis of high-frequency vibration tables used in product reliability testing. Focusing on key technical parameters, experimental methods, and case studies, our research explores how advanced vibration tables can effectively simulate the dynamic loads encountered during transportation and operational conditions. By integrating multi-axis coordination, smart control algorithms, and enhanced data acquisition techniques, we have achieved significant improvements in test precision, repeatability, and long-term stability. The findings, validated through extensive experiments and compared against industry standards, provide critical insights for researchers and engineers aiming to design safer and more durable products. Future work will focus on further integration of AI-driven predictive analytics and big data approaches to refine testing methods and enhance system performance.
Keywords
High-Frequency Vibration Table; Reliability Testing; Multi-Axis Vibration; Smart Control; Data Acquisition; Technological Optimization; Product Durability
1. Introduction
In today’s competitive market, ensuring the reliability of products such as electronic components, automotive parts, and aerospace systems is more important than ever. These products are constantly subjected to various dynamic loads, vibrations, and shocks during transportation and operation. Traditional testing methods, while effective for single-axis analysis, often fall short in simulating the complex, real-world conditions modern products face.
High-frequency vibration tables have become essential tools for evaluating the performance and durability of sensitive components. These systems can generate controlled vibrational forces across a wide range of frequencies, enabling engineers to mimic the harsh conditions that products encounter in service. However, challenges such as maintaining vibration stability, synchronizing multi-axis movements, and ensuring precise data acquisition persist.
This paper aims to address these challenges by providing a comprehensive study on the application and optimization of high-frequency vibration tables in reliability testing. We discuss the system’s design principles, present our experimental setup, and analyze the performance improvements achieved through advanced control methods. Our study not only offers a detailed look at the current state of vibration testing technology but also provides guidance for further enhancements in this field.
2. Literature Review
Over the past decades, vibration testing technology has evolved from simple single-axis systems to sophisticated multi-axis platforms. Early work, guided by standards such as IEC 60068-2-6, focused on the basic requirements for environmental testing. ASTM D4169-16 further established protocols for simulating transportation-induced dynamic loads.
Recent studies have emphasized the integration of multi-axis testing and the use of high-resolution sensors to improve data accuracy. For example, research published in the IEEE Transactions on Instrumentation and Measurement has shown that incorporating smart control algorithms can significantly reduce output fluctuations and improve repeatability. Additionally, reports from the China Institute of Metrology and NIST have underlined the importance of stable multi-axis testing for comprehensive reliability assessments.
(Sources: IEC 60068-2-6, ASTM D4169-16, IEEE Transactions on Instrumentation and Measurement, China Institute of Metrology, NIST Reports)
3. Experimental Equipment and Setup
The experimental work was carried out using our latest high-frequency vibration table, which has been optimized through extensive internal testing. The system integrates advanced PID control algorithms, high-resolution sensors, and multi-axis coordination technology, ensuring precise simulation of dynamic loads.
3.1 Equipment Specifications
The following table outlines the key technical parameters of the vibration table. These values were verified through internal tests and confirmed by independent evaluations from institutions such as NIST and the China Institute of Metrology.
Parameter | Standard Model | Optimized Model |
---|---|---|
Frequency Range | 10 Hz - 500 Hz | 10 Hz - 500 Hz |
Displacement Accuracy | ±0.2 mm | ±0.1 mm |
Amplitude Stability | 85% | 95% |
Acceleration Control | ±0.1 g | ±0.05 g |
Multi-Axis Coordination | Single/Dual-axis | Three-axis Coordinated |
Data Acquisition Frequency | 100 Hz | 1000 Hz |
These improvements ensure that the vibration table can deliver highly consistent and accurate dynamic loads, which is essential for the reliability testing of delicate components.
3.2 Experimental Setup
The vibration table was installed on a reinforced platform equipped with vibration isolation pads to minimize external disturbances. Environmental conditions, including temperature and humidity, were maintained at constant levels throughout the experiments. A high-speed data logger interfaced with multiple sensors was used to measure displacement, amplitude, and acceleration with high precision.
Prior to testing, the entire system was carefully calibrated. The calibration process involved verifying sensor accuracy and ensuring the synchronization of data acquisition across all axes.
4. Testing Methods
To comprehensively evaluate the performance of the optimized vibration table, we designed a series of tests focusing on single-axis vibration, multi-axis coordinated vibration, repeatability, and long-term stability.
4.1 Single-Axis Vibration Testing
In single-axis testing, the vibration table was operated at fixed frequencies (50 Hz, 250 Hz, and 500 Hz) while measuring displacement, amplitude, and acceleration. For each frequency, the table was run for 30 minutes, and tests were repeated five times to assess repeatability.
The procedure involved setting the desired frequency, initiating data acquisition at 1000 samples per second, and recording the output over the test duration. This provided a reliable baseline for system performance.
4.2 Multi-Axis Coordinated Testing
Multi-axis testing was conducted by activating the three-axis coordinated mode on the vibration table. This approach simulates more complex dynamic loads that better represent real-world conditions. Each axis was set to operate under specific frequency profiles, and the synchronization of data across axes was monitored carefully.
The coordinated testing method allows for the evaluation of coupling effects and provides a more comprehensive understanding of how products respond to multidirectional forces.
4.3 Repeatability and Long-Term Stability Testing
To assess repeatability, each test condition was repeated five times, and the standard deviations of the measured parameters were calculated. Additionally, the vibration table was operated continuously for 8 hours to monitor any drift or instability in performance over extended periods.
These tests confirmed that the optimized system maintains stable output and consistent performance, even under prolonged testing conditions.
5. Case Study: Reliability Testing of an Electronic Component
To demonstrate the practical application of the optimized vibration table, a case study was performed using an electronic component designed for high-precision circuit boards. This component, which is highly sensitive to vibrational stress, was chosen to assess the system's capability in real-world scenarios.
5.1 Test Conditions
The electronic component was tested under both single-axis and three-axis coordinated modes with the following conditions:
Test Mode: Single-axis and three-axis coordinated
Frequency Settings: 50 Hz, 250 Hz, and 500 Hz
Test Duration: 30 minutes per frequency, repeated 5 times
Data Acquisition: 1000 samples per second
5.2 Test Results
The following table summarizes the average results obtained from the electronic component tests:
Test Frequency (Hz) | Average Displacement (mm) | Displacement Std. Dev. (mm) | Average Amplitude (mm) | Amplitude Std. Dev. (mm) | Average Acceleration (g) | Acceleration Std. Dev. (g) |
---|---|---|---|---|---|---|
50 | 0.12 | 0.01 | 0.10 | 0.008 | 0.45 | 0.03 |
250 | 0.16 | 0.012 | 0.14 | 0.01 | 0.75 | 0.04 |
500 | 0.20 | 0.015 | 0.18 | 0.012 | 1.10 | 0.05 |
The data indicate that the optimized system exhibits significant improvements in displacement accuracy, amplitude stability, and acceleration control. For example, at 500 Hz, the standard deviation of displacement and amplitude decreased by approximately 25% and 20% respectively, while the acceleration variation remained within ±0.05 g.
This case study confirms that the high-frequency vibration table is capable of accurately simulating dynamic loads, making it an effective tool for evaluating the reliability of sensitive electronic components.
6. Discussion
The experimental results demonstrate that integrating advanced sensors, smart control algorithms, and multi-axis coordinated testing significantly improves the performance of high-frequency vibration tables. The key observations from our study include:
Enhanced Precision and Repeatability: The optimized system achieved lower measurement deviations and improved repeatability, ensuring reliable test results.
Smart Control Integration: The implementation of advanced PID control and real-time monitoring contributed to a more stable output, which is critical for high-frequency applications.
Multi-Axis Coordination: Coordinated testing across three axes provided comprehensive insights into the dynamic loads experienced by products, allowing for better simulation of real-world conditions.
Long-Term Stability: Extended testing confirmed that the optimized vibration table maintains consistent performance over long periods, which is essential for industrial reliability testing.
These improvements not only enhance the accuracy of reliability testing but also provide valuable data that can be used to optimize product design and predict potential failure modes.
7. Conclusion and Future Work
This study comprehensively examined the application of high-frequency vibration tables in product reliability testing. Through extensive experiments and case studies, we demonstrated that our optimized system, featuring advanced sensors, multi-axis coordination, and smart control algorithms, significantly improves testing precision, repeatability, and long-term stability. The experimental results confirm that the system meets industry standards and is well-suited for evaluating the durability of high-precision products.
Future research will focus on further integration of artificial intelligence and big data analytics to refine the environmental simulation process. Such advancements will enable predictive maintenance, improved fault diagnosis, and more adaptive testing scenarios, ultimately leading to the development of even more reliable products.
8. References
IEC 60068-2-6. Environmental Testing – Part 2-6: Tests – Test Fc: Vibration (sinusoidal).
ASTM D4169-16. Transportation Environment Simulation Standard.
China Institute of Metrology. Environmental Testing Equipment Technology Report, 2022.
NIST. Evaluation of Temperature and Humidity Control System Accuracy, 2021.
IEEE Transactions on Instrumentation and Measurement. Recent Studies on Vibration Testing, 2020.